Onboard the USS Ford- The aircraft carrier USS Gerald R. Ford (CVN 78) represents many firsts – new design, new electrical system, new propulsion plant, new aircraft launch and recovery system, new radars, new elevators and more. That the world’s most expensive warship ever built has teething troubles is well known, and that’s putting it mildly. During the Ford’s first operational period between mid-2017 and mid-2018 the carrier spent only 81 days at sea, and ten times had to cut short testing periods to come home with a serious problem. The Navy and its contractors were exceptionally mum about the detailed nature of many of those problems, stung by a never-ending stream of criticism from Congress and a host of media, commentators and analysts.
The Ford has now returned to service after completing a 15-month post-shakedown availability (PSA) that began in July 2018. The PSA, a planned dockyard period to fix expected problems and install additional gear not specified in the original contract, was even more intense than usual as contractors from Newport News Shipbuilding, General Electric, Raytheon, General Atomics and more, along with employees from a host of Navy laboratories and research facilities, worked to correct many of the deficiencies that arose in the initial operating period. The Navy has not publicized much of that work, in line with a policy to not show much of the ship or even to allow media on board while underway during the initial operating period.
But as the ship backed from its pier at Newport News, Virginia on Oct. 25 to begin post-PSA sea trials, the Navy pulled aside some of the veil of secrecy that has shrouded the 100,000-ton ship. Videos and photography of the refurbished Ford appeared as the events were taking place and, unlike before, the taxpaying public got a better look at their $13 billion to $15 billion investment.
In late November the shroud lifted just a bit more, and a small group of reporters was allowed on board for a few hours as the Ford was headed back to Norfolk from 20 days of underway tests. It was the first occasion where media got a chance to visit the carrier while at sea and watch and talk with her crew as they operated and tested their ship.
And it seemed – at least from the few hours we had on board – that a genuinely new spirit is around the ship and the program. In Washington the Ford class effort is often characterized as doom and gloom, rife with concerns and intense oversight. But on the Ford herself folks seemed determined to make it work.
“I feel frustrated by that but the sailors do not,” Capt. John J. “Yank” Cummings, the carrier’s commanding officer, said of the Ford’s reputation. “Morale of the ship is good now that we’re not wearing hard hats and we’re seeing that the equipment that was worked on [in the shipyard]is now working. We’re going to turn it around and make it happen, and these last twenty days have been a big step in making that happen.”
Our visit was brief but we in packed in a lot. We watched a demonstration of one of the advanced weapons elevators (AWE), a significant innovation that substitutes electromagnetic drives for the hydraulic systems that power most elevators. We saw one of the electromagnetic aircraft launch systems (EMALS) being tested with dead-load shots. We moved by a plane-handling tractor pulling an arresting cable to calibrate tensions for one of the three advanced arresting gears (AAGs). We walked the huge aircraft hangar and stood on the flight deck as the ship heeled to change course. We visited the bridge where a full watch team worked to guide the nearly 1100-foot-long ship back to port. And we talked with sailors tasked with the responsibility to operate those systems.
“We’ve operated the elevators over a thousand times while we’re out now,” said Lt. Cdr. Chabonnie Alexander, the ship’s ordnance handling officer, as he stood by Upper Stage Weapons Elevator No. 3, one of eleven AWEs on the Ford. “They work.”
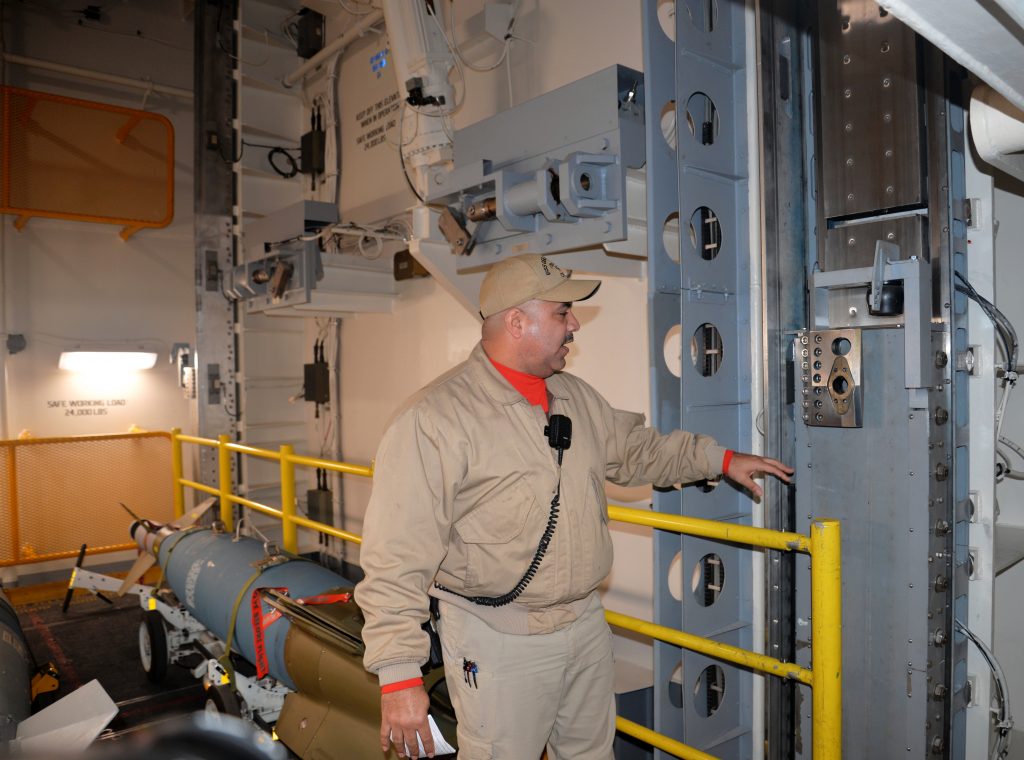
Ordnance handling officer Lt. Cdr. Chabonnie Alexander explains the operation of a permanent magnet motor that drives Advanced Weapons Elevator No. 3. (Chris Cavas)
Early on in the Ford’s development the EMALS launch and AAG recovery systems and the dual-band radar (DBR) were the innovative systems that got the most attention, but over the past two years it’s been the elevators that have come under the most scrutiny.
No. 3 is one of three upper stage elevators which, along with a supply elevator, have been recalibrated and checked out by engineers and contractors and returned to the crew – “turned over” in Navy parlance — for regular operation. Those four AWEs transfer weapons from assembly rooms, where bombs and missiles brought up from magazines deep within the ship are prepped before use, up two or three decks to the flight deck where they’re loaded onto aircraft.
The configurations of the seven lower-stage elevators are more complex, carrying weapons up five or more decks from the magazines to the assembly rooms. None of those seven AWEs have officially been turned over to the crew, but a couple are close and are being routinely operated.
Engineers from Newport News Shipbuilding, who oversee the elevator installation, were aboard the Ford for sea trials and during the current at-sea periods. At one point during sea trials the engineering team suggested a change in plan as the ship encountered relatively heavy seas.
“The folks from Newport News were so creative that during full power trials they said let’s run the elevators from top to bottom, including one not turned over to the ship,” said Rear Adm. James Downey, Program Executive Officer Carriers for Naval Sea Systems Command, who was aboard for the trials and during our visit.
“The elevators need to operate in Sea State 5, that’s the overall requirement,” Downey said. “And they worked, no issues with those elevators in moving situations, even with the elevator that wasn’t complete yet.”
“We ran that lower stage elevator thirty to forty times in heavy seas, no issues,” Cummings chimed in. “We’ve run a thousand cycles on the elevators – four upper stage and one or two lower stage — over these last three days in seas ranging from zero to 18-foot plus seas are, with no issues.”
The demonstration we witnessed of No. 3 AWE also included operation of the massive, armored doors and hatches that protect the ship in the event of an explosion inside the elevator well. The doors are on the vertical sides of the elevator well and horizontally in the decks and flight deck. They are complex affairs and very heavy.
That complexity was on display during the demonstration. Sailors on different levels coordinated with each other to synchronize the opening and closing of the armored doors before engaging the permanent magnet motors that drive the elevators. The sequences are run each and every time the elevators move.
“All the elevators are different, based on maximizing the number of bombs in the ship,” Downey said. “They differ in their doors, hatches and designs so we can fit as many bombs in the magazines as possible. We’re going through those most complex elevators first – lower stage five, lower stage seven and lower stage one. And using those elevators as risk-reduction efforts on board the ship so we understand what the modifications are.
“Most of the [elevator]issues we’re working on completing are not related to the technologies involved,” he added. “We’re not working on issues related to the permanent magnet motors, to the movement of the platform. We are working on the structural fit-up of the doors and the hatches and that movement of those multi-ton doors. The doors have very tight survivability specifications, thousandths of an inch on a multi-ton door, how it interfaces with the hull, airtight, watertight. And as you work on a door like that you can work quite a while.”
The Ford design is intended to produce a significantly higher sortie rate than the preceding Nimitz class, an individual sortie representing a single aircraft launch and recovery. The faster that aircraft can be loaded and launched, the more bombs and missiles can be put on target. Nimitz carriers have a sortie rate of 120 a day at normal sustained operations. The Ford is intended to generate 160.
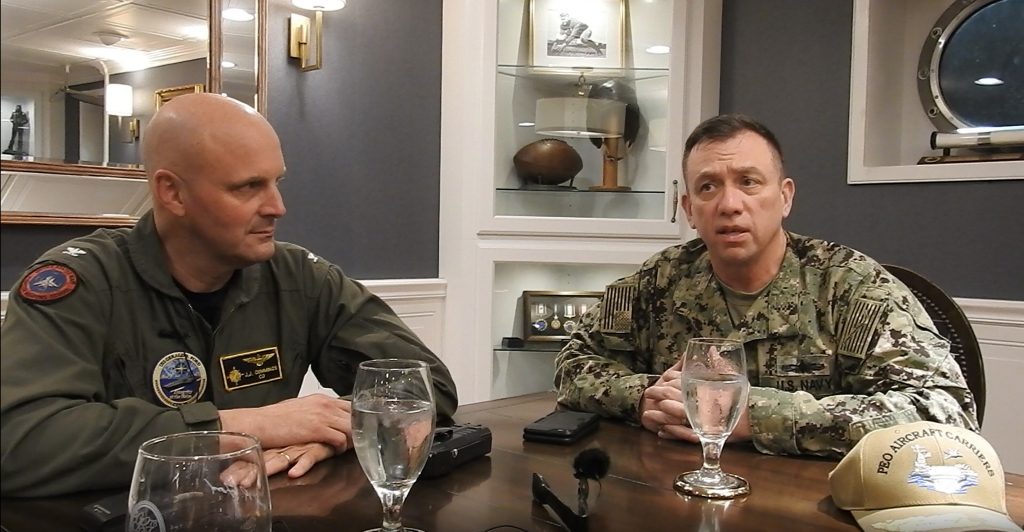
In the captain’s day cabin aboard the Ford, commanding officer Capt. J. J. Cummings, left, and Rear Adm. James Downey, Program Executive Officer for Carriers, talk about the ship’s progress and plans for the coming year. (Chris Cavas)
Key to hitting that rate, Downey said, are the AWEs. But while two lower-stage elevators are expected to be turned over by spring 2020, it could be another year before all eleven are in full working condition.
That schedule fits the overall plan to get the ship through the test and trial period expected to last into the spring of 2021. One reason it will take so long, Downey said, is that the ship is intended to be at sea half the time over the next eighteen months or so. There are also other systems that need to be checked out and perfected before the entire AWE system will be needed.
“We didn’t leave [full elevator testing]for the shipyard period because we wanted to exercise the ship,” Downey said. “We wouldn’t have exercised the propulsion plant, we want to certify that the [advanced arresting gear]water twisters work and we can go ahead and start launching and recovering aircraft. We wouldn’t have been able to energize the dual band radar.
“Candidly the ship does not need all eleven elevators to do combat operations,” he added. “They have redundancy or additional capacity. So our goal is to get all the testing done by spring 2021 and then go into shock trials with a completed ship.”
The operating periods since returning to sea have focused on getting the ship ready, and with the new year, Cummings and Downey said, the Ford will concentrate on aircraft operations. To that end the EMALS and AAG systems are being tested and run through their paces before aircraft are brought on in January.
“We conducted 747 [aircraft]launch and recovery cycles during the initial operating period” in 2017 to 2018, Downey said. “We will be doing thousands in 2020.”
The qualification cycle will begin with T-45 two-seat training aircraft flown by experienced pilots, he said, followed by C-2A COD Carrier On-Board Delivery cargo aircraft and then F/A-18 E and F Super Hornet strike fighters. As flight operations progress more attention will focus on the EMALS and AAG systems launch and recovery.
An impromptu discussion took place with about a dozen sailors as we walked through a generating room for the electromagnetic launch system. Concerns persist the EMALS system won’t regenerate power fast enough to hit the sortie rate and that the system will need to power down periodically to recover from a high rate of operation.
“No,” several sailors who operate the system adamantly declared when those worries were raised. “The system works. It will work as fast as we can load aircraft onto the catapults.”
The EMALS system consists of four generators cross-connected to each of the ship’s four catapults. All four generators power each launch and are cycled from catapult to catapult as planes are flown off. The system needs only a fraction of a second to make the switch, the sailors said, adding the time lag was “not a problem. It’s virtually instantaneous.”
Another sailor pushed forward to join in.
“We know the system works,” he declared. “We need to tweek it and understand its complexities, and the more we run it the better we’ll get. We just need to operate it.”
Everyone in the room nodded up and down in agreement.
A similar confidence was expressed in Advanced Arresting Gear Engine Room No. 2, where Chief Aviation Boatswain’s Mate Launching and Recovery Reginald Leonard explained the operation of the AAG engines and the water twisters that are key to the system’s ability to bring landing aircraft smoothly and quickly to a halt. At issue has been the robustness of the water twisters that are intended to operate 25 years before replacement.
All six water twisters – two on each of the ship’s three arresting wires – were sent back to General Atomics to be remanufactured during the Ford’s overhaul, Leonard told us. Since then, he said, the system is proving much more reliable, and he expressed confidence the AAGs will work as advertised.
“As we get operational there are still a lot of questions we have as operators,” Leonard said. “We really need to operate to push this equipment to its limits so we can see what it can do and how we respond.”
“We’re very confident that this stuff works,” Downey added. “I don’t say that lightheartedly. We’ve operated it enough to know that it works. But what to do for the 50-year life [of the equipment], that’s really the big challenge for us.”
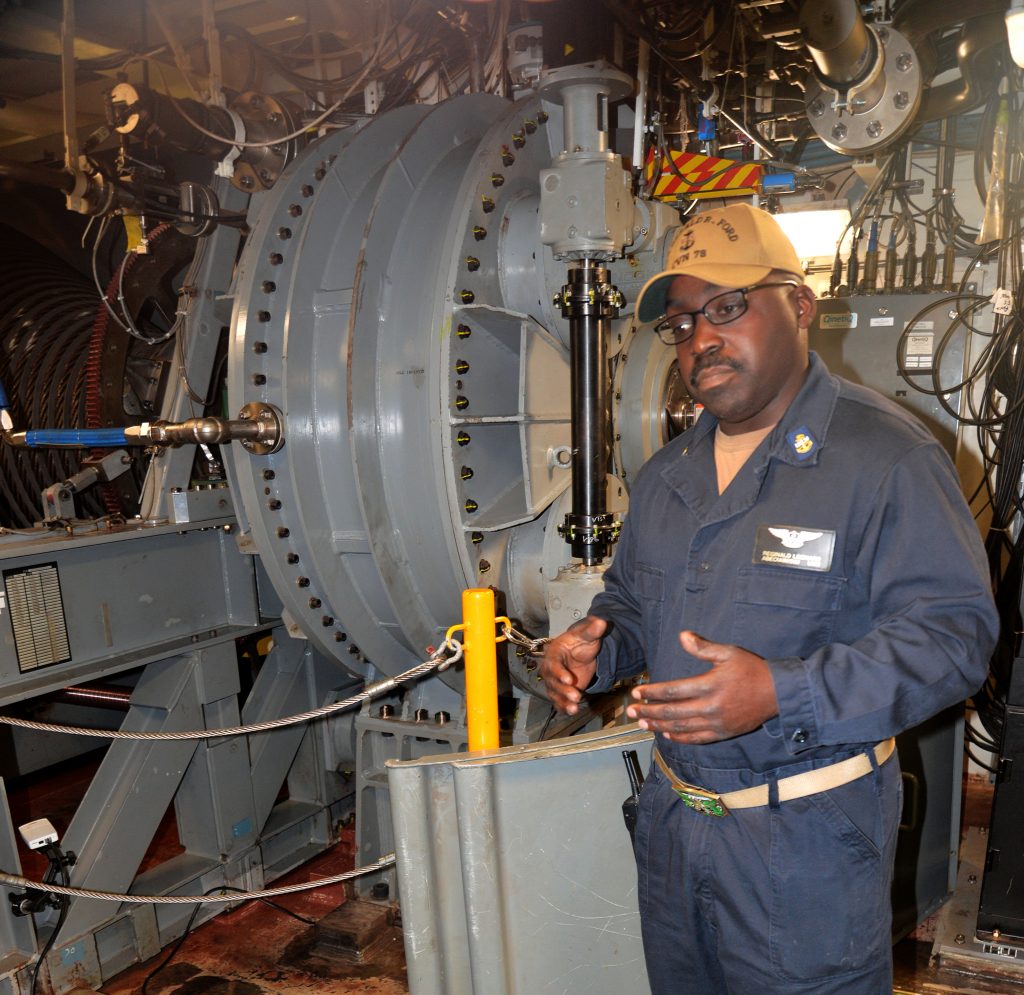
Chief Aviation Boatswain’s Mate Launching and Recovery Reginald discusses operating the Advanced Arresting Gear in AAG Engine Room No. 2. (Chris Cavas)
After the ship moored at Norfolk Naval Base Downey and Cummings spoke in more detail about the propulsion system problems addressed during the PSA, where work was done on the main reduction gear thrust bearings, and how the overhauled power plant performed during sea trials.
The work done was “principally throttle control work and main reduction gear thrust bearing work,” Downey said, brushing aside rumors that large machinery elements were removed and replaced. “The team was able to design and engineer the bearing area in place. There was not any removal of the MRG thrust bearing,” he said. “The interface had to be remachined.”
During post-PSA sea trials, “the ship performed exceptionally,” Downey said. “Crashbacks, full ahead, full astern, full rudder sequences.”
“The engines and shafts worked perfectly. No issues whatsoever,” Cummings chimed in.
“Imagine a 100,000-ton ship stopping in four ship-lengths,” Downey added. “Automatic throttle settings. From ahead flank, as fast as we can possibly go, to as fast astern as we can possibly go. And it operated extremely well.”
“No issues,” Cummings said again.
The Ford was back to sea for a few days more in December before returning to Norfolk. Downey and Cummings were adamant the ship will be underway throughout 2020 proving itself.
“For us, it’s get to sea, exercise the ship, get the air wing on board and work through all those issues,” Downey said.
“We have proven on the last two underways that we can do ship things,” said Cummings. “Now it’s time to prove to the Navy we can do aircraft carrier things.” ■
Posted 19 Dec 19
Email at chriscavas@gmail.com